Team in action!
MedLaunch Independent Art Studio Setup
Role: Design Strategist
Team: Vik Mehan, Kaitlyn Ford, Ruma Deb, Emily Goetzler, Emily Greatorex
Timeline: September 2019 - May 2020
Project overview
MedLaunch is an organization on campus that works at the intersection of design, science and technology to solve healthcare problems.
6 years ago, James Murtha suffered a mountain biking accident and became a C4 quadriplegic. Unable to achieve any mobility below the waist and having limited mobility below the neck, James had a difficult time pursuing a number of his hobbies including painting. Although he’s a skilled painter, he is unable to paint without assistance from another person. With 1 in 50 people experiencing paralysis, that results in 5.4 million people having difficulty utilizing a creative outlet to express themselves. James wanted a way that he can paint and create art independently, allowing him to creatively express himself and relieve stress and anxiety.
Problem statement
Quadriplegics and others with limited mobility of their arms need a solution that will enable them to set up their paint supplies independently.
James Murtha, community partner
Interviews, Observations, & Market Research
We first spoke with James to learn more about his condition and exact needs. We asked him to walk us through how he would normally set up his studio and paint.
As a result, we learned that he actually doesn’t have a problem painting, but rather wants a way to set up his paints without additional help.
Additionally, we conducted competitive research, yet found that there was no existing art studio tool in the market that would enable quadriplegics to paint independently.
James’ current setup
Insights
Design requirements
Ideation and sketches
Design iteration #1
James uses acrylic paint, thus with our initial sketch, we realized the paint would likely dry up on the surface that opened the tubes that held the paint.
We also realized that because the paint was thick, gravity alone would not force the paint out of the tubes.
Thus, with the design constraints in mind, we decided to experiment with automatic soap dispensers as a solution to distribute the paint on a pallet. We envisioned that the dispensers would be placed on a rotating lazy suzan stand with a palette attached to it by an extendable arm.
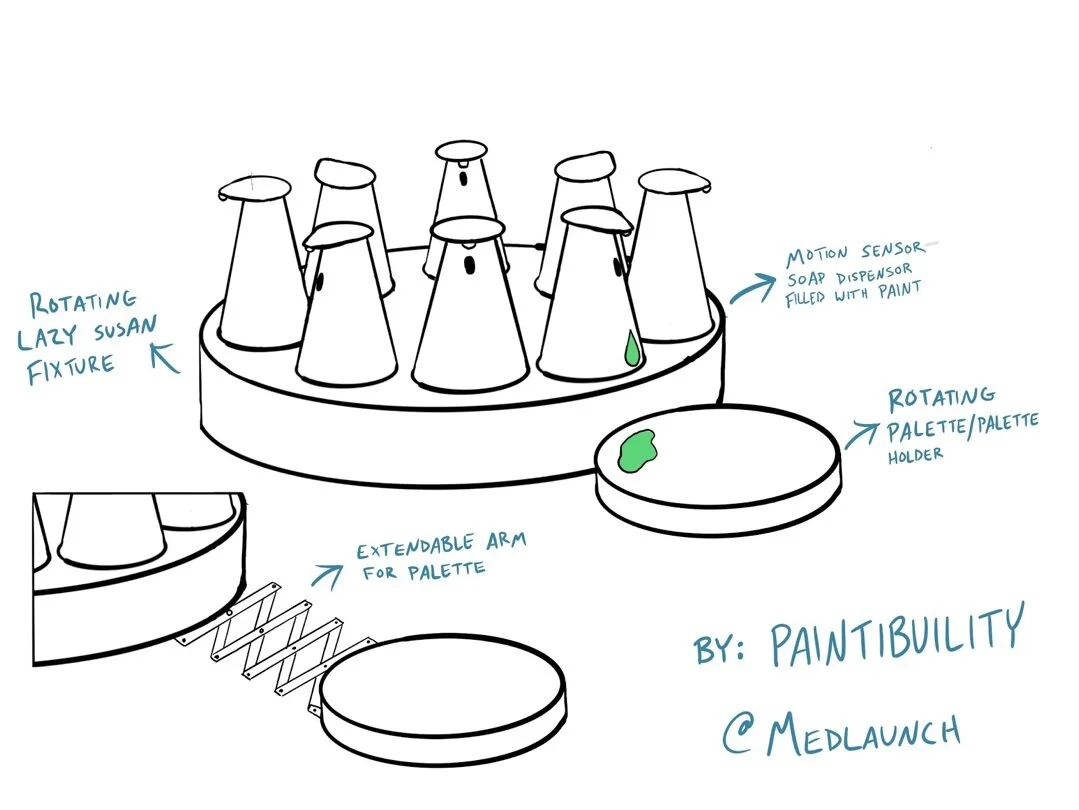

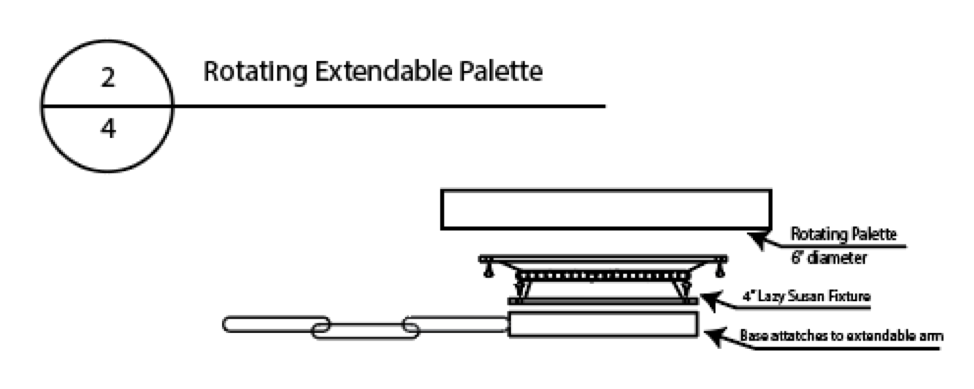
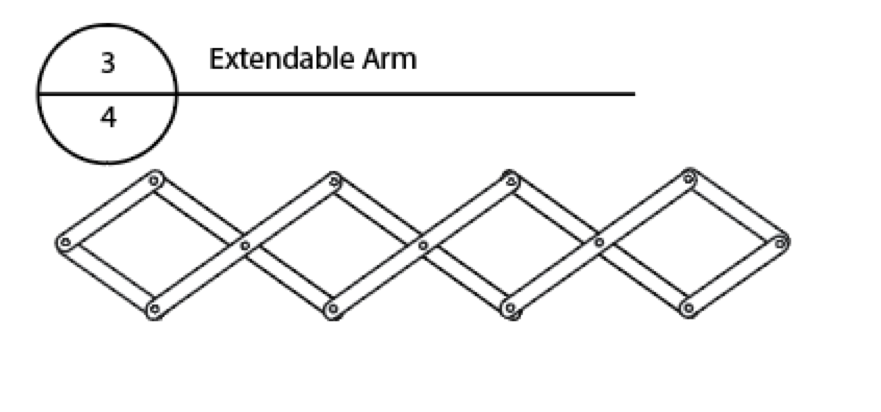
Testing
Prototype
Points of friction
1. The paint was too thick to travel up any manufactured automatic soap dispensers.
2. Some manufactured soap dispensers were poorly made, unreliable, and inconsistent. They could also easily cause a mess.
Feedback (from James and other experts)
1. James mentioned that he wanted ridges on the side of each pallet, which will provide a way for him to grip and turn them easier.
2. James also said that he desired a drip catcher underneath the paints to catch any excess paint that falls.
3. One professor suggested that motion sensors are too faulty and we should start our design with regular soap pumps as an alternative.
4. Another expert advised that we connect all the sensors together with an electronic wire.
Design iteration #2
Our second design still used a carousel, but instead of motion sensors we planned to use buttons on top of our dispensers. Also, we flipped the dispenser on its head. Instead of paint being pumped from the bottom to the top as in a soap dispenser, we decided that we could pump the paint out of the bottom of the bottle by increasing the air pressure in the top and adding a tube at the bottom for the paint to come out. This design used a mini air pump to push air in the top, which would increase the air pressure in our bottle and force paint out of the tube at the bottom. This design worked to push paint out, but a problem we came across was that the tube at the bottom leaked a small amount of paint. This would easily cause a mess for James and was the next problem we needed to solve.
Designed in collaboration with Emily Goetzler
Testing
Design iteration #3
In our most recent iteration, we used the dispenser design with improvements to prevent leaks by adding a solenoid valve. It only opens when the mini air pump is running. It closes when the air pump stops running in order to prevent excessive paint from leaking out.
We met with James again to gain his input. In our meeting with him at his parents’ home, we decided on proper heights for the stand. We also confirmed the buttons and palettes in our design. We decided to remove the carousel and rotating feature and make this a static design of 6 dispensers in a 3x2 grid pattern, as the carousel would have taken up more space than was necessary.
We planned to have 6 dispensers in a portable box which can be plugged into a wall outlet to power the pumps and valves. Each dispenser would have a button on top of it so that James can hit the button of whichever color he wants and the paint will dispense as long as he holds the button down. The paint would dispense into a disposable aluminum palette and be able to be pulled out from a drawer underneath the dispensers so that James can bring the paint to his canvas.
Reflection
Key takeaways
Challenges
Identify all requirements before you start prototyping.
During the design process, we realized that we lacked some important information and context that guided many of our decisions for our final designs, including the number of paints James uses, how he cleans his brushes, how often he paints, etc. Thus, when designing, I realized that you have to be able to quickly adapt to new requirements and stay open to new ideas as constraints often arise during the brainstorming process.
Our design process required an immense amount of flexibility as we had multiple design shifts and changes. It was crucial to quickly iterate and adapt in order to continue advancing and improving our project to better align with our community partner and goals of the team.
It was challenging to communicate our design ideas to one another, thus we found that actually sketching them out and using a whiteboard was the best way to visualize each other’s thoughts.
COVID-19 setback, as this slowed our work on our physical model as we couldn’t meet as a group in person and had limited access to 3D printers and power tools to fully fabricate our design.